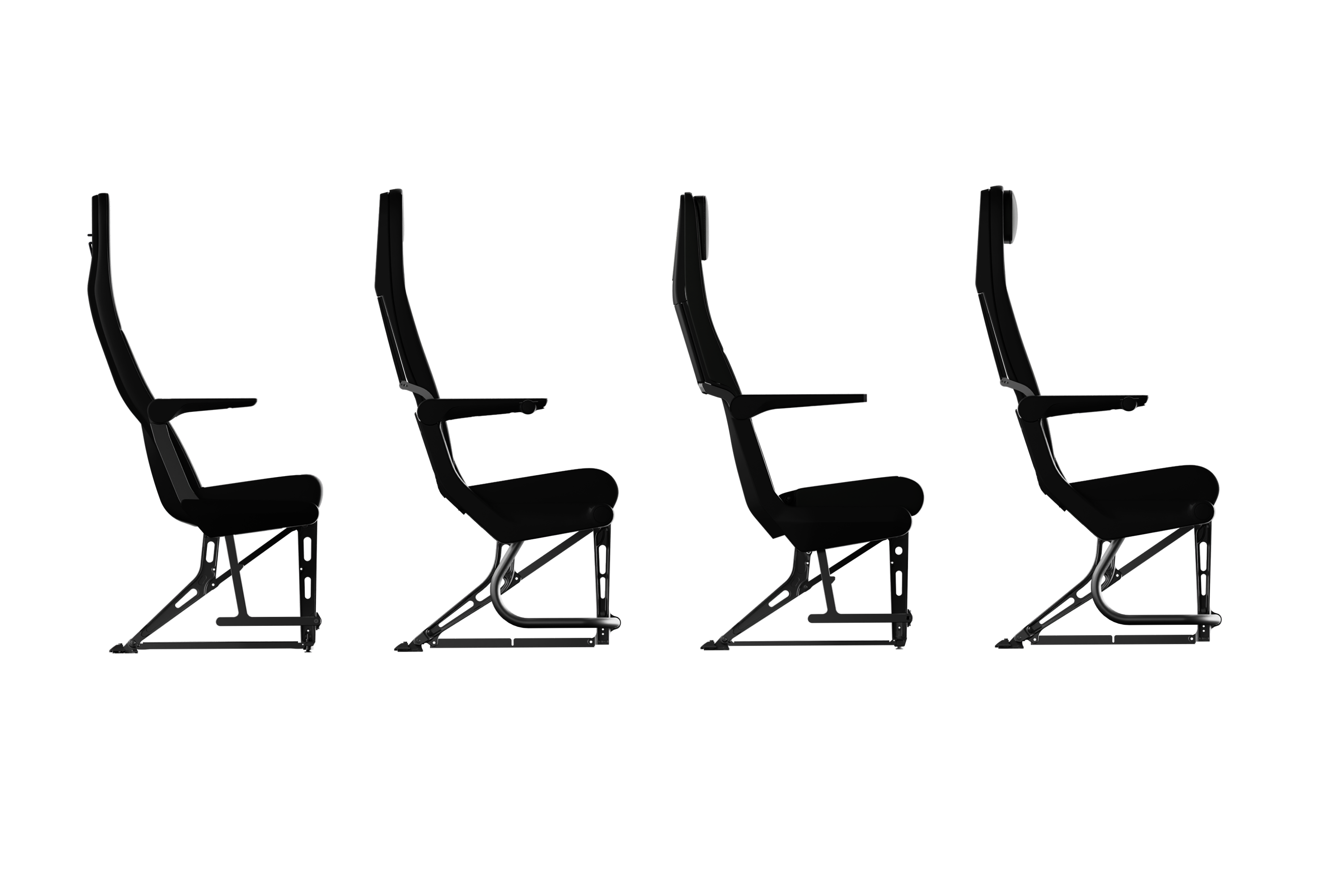
Our vision is to bring together the technologies, expertise, and best practices from the automotive and aerospace sectors to deliver innovative, high-performance aircraft seating products.
Our mission is to reliably deliver innovative aircraft seating whilst enhancing customer experience.
A heightened industry perspective.
Ben McGuire, CEO
An atmosphere of excellence.
An approach that goes beyond a physical product, at Mirus Aircraft Seating our processes prioritise a higher standard of service at every level.
Collaborations over transactions.
Assets built to last — aircraft seating and business relationships alike. While our approach to engineering focuses upon agility, innovation, creativity and quality, our service is centred wholly on people. It is in our DNA to work with our customers to build a product that meets individual brand requirements. Our team will work with you to incorporate your values into our products, helping to produce more memorable passenger experiences and solidify a truly collaborative experience.
Primed for take-off.
Our fully-integrated, state-of-the-art production system intertwines with a ground-up approach to quality systems and supply chain management; ensuring industrial reliability, speed and scalability.
Committed to delivering aircraft seats quickly and efficiently, our standard seat lead-time is 6-8 weeks (assuming no modification is required). We also offer a fast-track dispatch service where we hold a limited number of seats in stock.
Production without compromise — we use quality assurance tools tailored to aerospace-specific requirements alongside the latest automated process control technology to ensure error-proofing, repeatability, waste reduction and products of the ultimate calibre.
From first sketch to final fit-out.
An entirely full-service production, every aspect of bringing our aircraft seats to fruition is an in-house process. From design brief and concept sketching to prototyping, testing, certification, manufacturing, and finally, delivery and aftercare support — our team personally shapes your product at every phase.
- CAE – static and dynamic simulation capability
- Testing – Dynamic test rig, static and cyclic, flammability
- Design, Development, Certification, Manufacture, QC
- Composite component manufacturing capability – kit cutting, press curing, trimming
Thinking of tomorrow.
A vision for environmental responsibility executed from day one. At Mirus we seek to proactively minimise the environmental impacts from our own operations, as well as play our part in reducing aviation’s impact on the global environment.
As a leading manufacturer of aircraft seats, with innovation at our core, we are well placed to ensure the products we develop contribute to achieving greater sustainability. Our seats are amongst the very lightest available and this helps our airline customers reduce fuel burn and CO2 emissions. Our seats are also amongst the most robust and most reliable in-service, which means reduced spare parts manufacture and logistics. When a part is required to be replaced, our seats are designed so components can be easily separated into constituent parts for ease of recycling through careful use of adhesives and mechanical fastenings. Functions that are only enabled by our continual investment in our state-of-the-art facilities and technologies.
“For each seat we produce, we use less energy, generate less waste and emit less carbon”
– Adam Challenor, Technical Director
Igniting innovation.
Mirus operates with a history and pedigree in the aerospace and automotive sectors. By drawing on the very best practices from both, we offer what we believe is one of the most specialised and compelling value propositions in the industry.
Big thinkers functioning without fear of failure, our culture cultivates ingenuity at every touchpoint. From highly collaborative design teams to specialists with diverse backgrounds and expertise to never-stagnant development processes, innovation sits at the core of our operation. An attitude only strengthened by our in-house dynamic testing capabilities, our designs are constantly optimised to feed innovation, reduce weight, and improve sustainability.
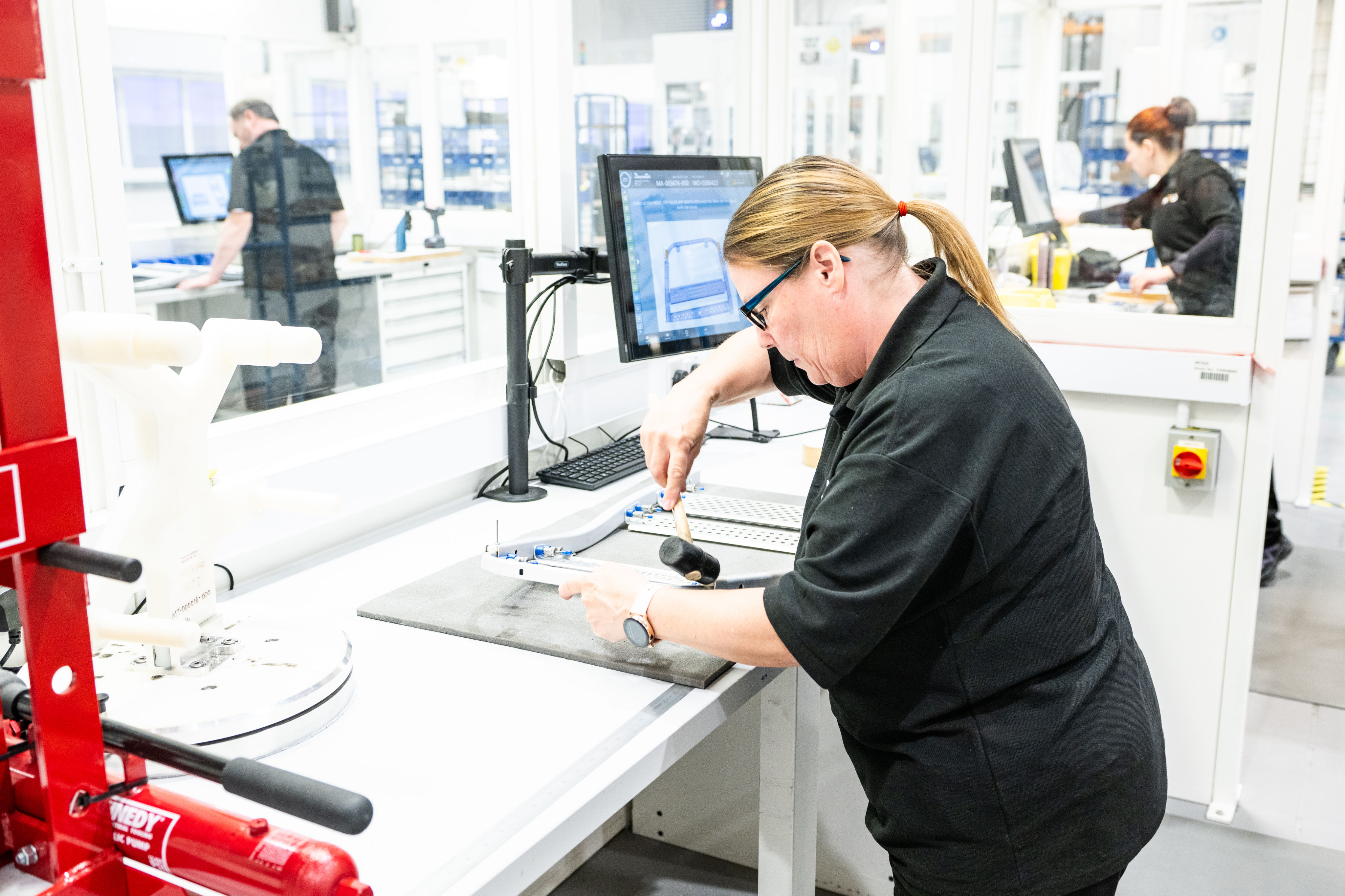
Looking to grow your career in a team fuelled by ingenuity?
Join usOur journey has only just begun.
Disrupting and reshaping the aircraft seating industry takes design flair, technical skill, a relentless commitment to excellence in all aspects of our business, and most of all, time. It’s a journey, but we’re well on our way.
2015
Founded February 2015
Moved into Hingham HQ, May 2015
2017
1st AirAsia retrofit seats flying
Part 21G approval received
2018
AS9100D accreditation received
2019
1st delivery to Airbus FAL
1st Boeing 767 EIS
ADOA approval received
Airbus OEM approved
2022
1st Americas airline customer secured
1st Middle East airline customer secured
MTEST facility opens
2023
Kestrel seat launches
ISO 17025 (MTEST) accreditation received
Mirus China consolidation centre goes live
2024
Kestrel Seat selected in the Airbus A320 BFE selection catalogue as a future product.
Hawk Infinity Seat selected in the Airbus A320 BFE selection catalogue as a future product.
Secured our first A330 programme
2025
Secured First Kestrel Customer
Hawk Duo launched at AIX 2025