In The Seat | James Wright, Operations Director
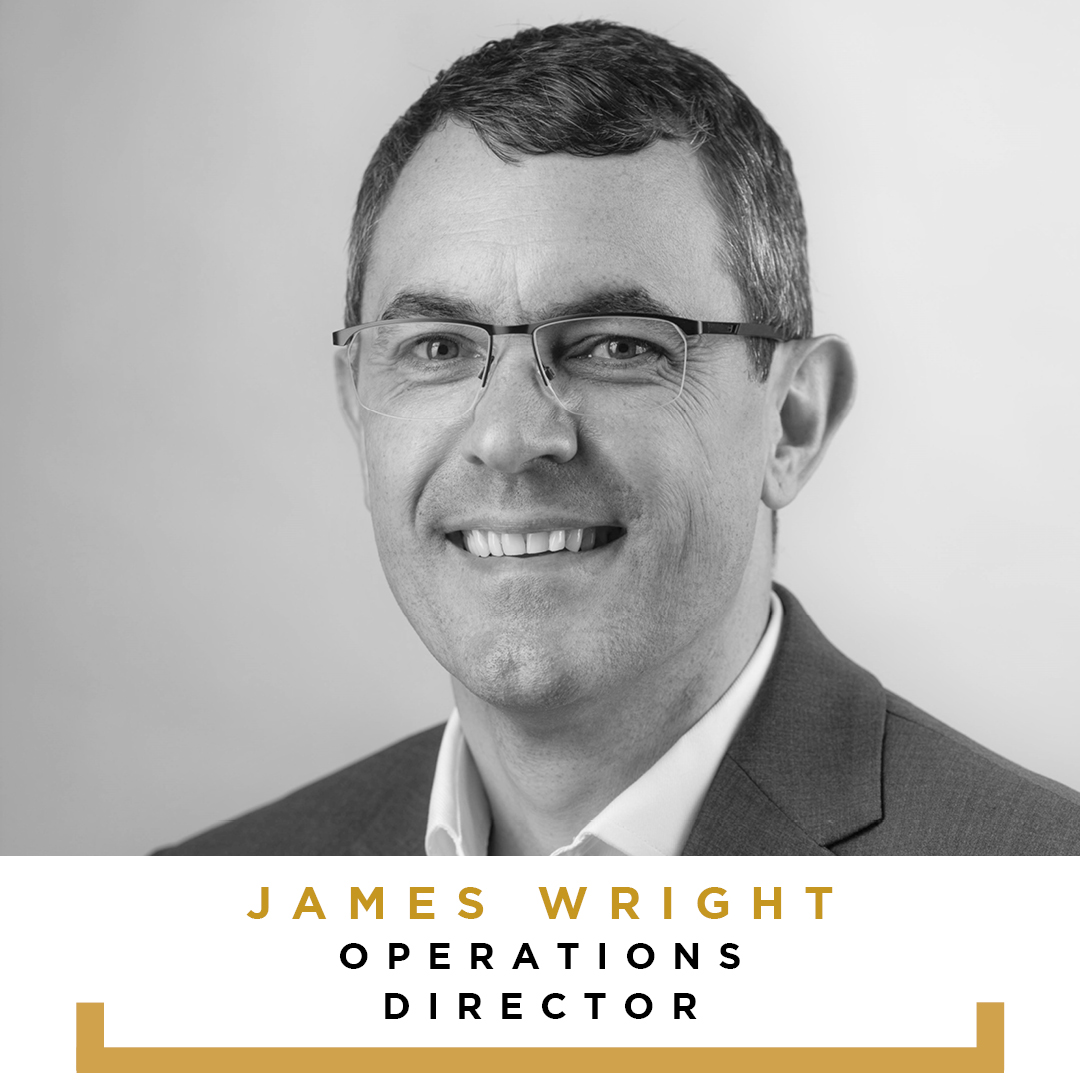
Continuing our 'In the Seat' series, where we are talking to and getting insight into some of the incredible people working here and driving Mirus forward. From Commercial, Certification, Product Design, Quality and Engineering we are lucky to call some of the most experienced and talented people in the industry our colleagues.
Next up in the series we are talking to our Operations Director, James Wright
In a pivotal role as Operations Director at Mirus, what does your role involve?
I am honoured that my primary role as Operations Director, is shaping the future of Mirus alongside the senior leadership team here.
I oversee all operational aspects of our company policies and business strategy working with our teams in production, distribution, supply chain and purchasing to help set goals to deliver the Mirus vision.
As well as directing and co-ordinating the internal structure of Mirus to ensure an efficient working environment, and that our deadlines are consistently met, I like to keep up-to-date on the latest industry developments so that we can remain competitive in our field.
Developing the strategic road map for Mirus has been to key to bring new capabilities and expand our production capacity to align with our business objectives and customer needs. It’s been great to support both the personal growth of individuals and teams within Mirus ensuring a solid platform that contributes to our success and growth.
You’ve worked in aviation for more than a decade, tell us about this and how your journey lead you to Mirus?
When I started work within aviation, I was fortunate to join a rapidly growing commercial and defence aerospace business. This enabled me to understand the intricacies of initial and continuing airworthiness organisations. From there, I gained experience working internationally in sectors from engineered textiles, complex assemblies, harnesses and mechatronics on a full range of commercial, military, fixed and rotary wing platforms, also business jet.
With my background in continuous improvement and automotive operating principles, and the Mirus vision to lead the way in the implementation of automotive best practices into commercial aerospace manufacture, the opportunity here felt like the perfect fit for me.
How has the aviation sector evolved since you began your career in aviation?
The two biggest changes I’ve seen in the aviation sector are a greater emphasis on supply chain resilience and robustness. Triggered post pandemic, by the major OEM’s in response to the material shortages and delays effecting final assembly lines. Secondly, a strategic shift, especially from Airbus, towards automotive style design and manufacturing structured processes and techniques, and this is where I’m pleased to say Mirus leads the way.
At Mirus, our vision for environmental responsibility has been there from day one. We seek to proactively minimise the environmental impacts from our own operations, as well as play our part in reducing aviation’s impact on the global environment.
As a leading manufacturer of aircraft seats, with innovation at our core, we ensure the products we develop continue to contribute to greater sustainability. Our economy seats are amongst the lightest, with our class-leading Kestrel seat weighing just 6.9kg per pax fully dressed. The lighter we can make our seats, the more it helps airline customers reduce fuel burn and CO2 emissions to achieve their sustainability targets.
Although light, our seats are also robust and reliable in-service, which means a reduced need for spare part manufacture and logistics. When a part is required to be replaced, our seats are designed so that components can be easily separated into constituent parts for ease of recycling. This is enabled by our continual investment in our state-of-the-art facilities and technologies.
Sustainability and reducing environmental impact follows through to all our manufacturing processes too. With our operation being mainly assembly, we continue to reduce our impact with waste, packaging reduction and recycling programmes.
Tell us about some of the standout moments for you and your team so far at Mirus…
This year we were able to successfully resume production and delivery of our Airbus linefit programme, post pandemic, which was a significant milestone for Mirus. I’m delighted that we have been able to maintain 100% on time delivery since our programme resumption. This success has contributed to the introduction of our Kestrel and also Hawk Infinity seat into the Airbus A320 BFE selection catalogue as a future product.
What do you love about your job?
I enjoy working with the highly motivated change orientated people here. As a relatively young business in aerospace terms, we have, and are able to be highly agile and are driven to make positive changes. The environment we have created has enabled us to make significant improvements in a short period. Being able to work with customers and OEM’s in a truly transparent and collaborative way is refreshing. I’m certain that this collaboration and agility has played a significant part in Mirus’ entry into the Airbus A320 BFE catalogue as a future product.
Outside and alongside Mirus what do you enjoy doing..
Outside of work my focus is mainly around my immediate family. Having travelled and moved around the UK and Europe over the past ten years with a young family, it has really made me value and recognise the importance of having a strong family bond. We all like to enjoy as many leisure activities together as possible, from cycling, paddleboarding, badminton and a family favourite is skiing in the winter months.